Health and Safety
Ferrovial works hard to create risk-free environments for all employees, as well as for the users of infrastructures and services. Two principles govern their action: Target Zero and the idea that any accident can be avoided.
-
Frequency Rate (1) (2)
-25.0 % -
Severity Rate (2) (3)
-23.2 % -
Frequency rate with contractors (1) (4)
-16.2 % More than 216 million hours worked
(1) Year-on-year variation in the index giving the number of accidents occurring during working hours that lead to days lost, for every million hours worked.
(2) Includes Broadspectrum data for the full year 2016. The variation over 2015 excluding Broadspectrum results in a decrease of -8.4% in the frequency rates and -6% in the severity rate.
(3) Year-on-year change in the index giving the number of days lost as a result of occupational accidents for every thousand hours worked.
(4) Broadspectrum data not included.
MANAGEMENT COMMITMENT
In 2015, the Board of Directors of Ferrovial approved a new Health and Safety Policy for the whole company, establishing the objective of developing risk-free working environments, based on the conviction that any accident is avoidable.
The maximum executive level of Ferrovial supervises the functions and responsibilities in Health and Safety. Thus the CEO reports the information related to this matter periodically to the Board of Directors. In addition, in all the areas the person responsible for Health and Safety is part of the Business Committee. The annual meeting of Ferrovial Executives begins with this subject.
MANAGEMENT SYSTEMS
The company is committed to the gradual extension of standardized management systems in all business areas under corporate standards. The requirements have therefore been defined that the companies in the group must comply with to achieve an accident-free working environment.
Last year, a roadmap was established to align the management systems in each business area, taking into account the necessary resources and tools. The changes include a new reporting system that gives a greater weight to leading indicators, geared to strengthening the culture of Health and Safety, as a lever for change towards a new model for managing Health and Safety in Ferrovial.
In addition, as part of the roadmap designed to boost Health and Safety, minimum safety standards have been defined for each of the business areas based on an analysis of their critical risks.
Amey has implemented a new simplified management system in line with this scheme of mandatory minimums for significant risks and the requirements established in Ferrovial. At the same time, the IT platform has been renewed to make mobile access easier from work sites.
The company considers inspection, monitoring and participation in the workplace to be a crucial component. The Health and Safety Department carries out an exhaustive on-site monitoring of safety conditions. In 2016 this has led to a total of 81,634 inspections and audits, 52.3% more than in 2015.
All the Health and Safety measures designed to avoid any type of accident have maintained the declining trend in the frequency and severity indices in 2016.
WORKER PARTICIPATION AND TRAINING
The Ferrovial workplaces promote participation of all the workers in detecting insecure acts and situations. Motivational campaigns have been run so that the workers can propose new measures designed to improve conditions in the workplaces.
Ferrovial has spent years increasing its training efforts to involve workers increasingly in the common goal of creating risk-free workplaces.
The company has programs such as the SAFE (Safety Awareness for Ferrovial Employees) Project, whose aim is to involve all the employees in improving Health and Safety on site. Ferrovial Agroman has successfully implemented it in some projects. It affects executives, who demonstrate leadership in safety through specific visits; middle managers, who are appointed leaders and make SAFE inspections; as well as manual workers, who based on their experience in the workplace, make proposals for improvement in working conditions and/or implemented measures. The situations detected, along with those identified in the inspections carried out by the Health and Safety Department, are analyzed jointly with the site manager and the Health and Safety officers and expert assigned to the project, at the periodic meetings that define the actions to be taken to improve safety conditions.
In addition, Ferrovial Agroman Chile has run the Risk Aversion Test initiative designed to detect potential factors in the reactions and performance of workers on site, using tools approved by the Chilean government, interviews and a variety of tests. The critical teams are composed of those receiving the best scores and the rest improve in the advancement workshops. Using questions that project situations of danger is a way of detecting those who recognize certain situations as dangerous and those who consider them normal.
Amey’s Health and Safety Target Zero campaign has been recognized by the HR Excellence Awards 2016 with a first prize in the Most Effective Use of Internal Communications category. The initiative includes a number of communication actions, among them the audiovisual report “Please Wake Up”, which tries to help employees understand the emotional impact produced when an occupational accident occurs.
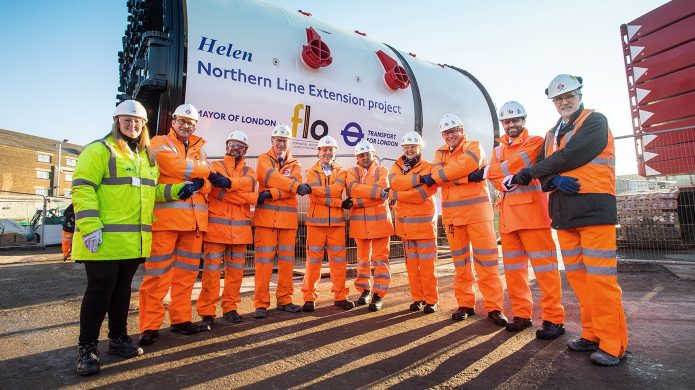
PHOTO: Workers of North Line Extension. London (United Kingdom)
ROAD SAFETY PLAN
In 2016 a Road Safety Plan was prepared, developing a Safe and Sustainable Mobility framework for all Ferrovial workers.
At the end of 2015, the company signed a collaboration agreement with Fesvial (the Spanish Road Safety Foundation) with the aim of reducing accidents “in itinere” and “in mission”. Fesvial is a benchmark in Spain in the area of road safety; its trustees include the Spanish Ministries of Interior, Employment and Health and the Madrid City Council.
In 2016 Cintra launched an international campaign with the message “Elige conducir de forma segura” (Choose to Drive Safely). The aim was to raise the awareness of employees and drivers that safe and responsible driving behavior can save lives. In the three months of summer, the campaign was focused on spreading road safety information via media such as posters, leaflets and videos. All this material was made known both physically along all the highways, and online through the websites (cintrasafety and ferronet) as well as via email and the social media.
COMMITMENT TO INNOVATION
Ferrovial believes that new standards of performance, technology and safety measures can be developed through innovation, contributing to the achievement of the aspirational “Zero Target” goal. Among the main lines of action in innovation, discussed in the section dedicated to this subject, is the application of technologies in the area of Health and Safety.
One example of this is the Warning Presence of People (WPP) to eliminate accidents in tunnels, where the interaction between man and machine is more complex. It combines sensor technologies (wearable devices) with localization in confined areas to produce a system of proximity warnings and alerts.
-
Hours of Health and Safety training (1)
940,585 +10,3% -
Health and Safety inspections and audits (1)
81,634 +52,3% -
Activity
85 % Under safety management systems
(1) Includes Broadspectrum data for the full year 2016. The variation over 2015 excluding Broadspectrum entails an increase of 0.67% in training hours and 9.44% in Health and Safety inspections and audits.
Milestones
- Establishment of a roadmap to align the management systems of each business
- Reduction in the frequency and severity rates
- Improvement in the process of reporting proactive indicators
20.19 Strategic CR Plan
Guarantee a safe and healthy working environment, developing action plans to improve the accident rates under the “harm-free workplaces” premise and involving the workers in Behavioral- Based Safety programs
'Yo cuido mis manos' campaign
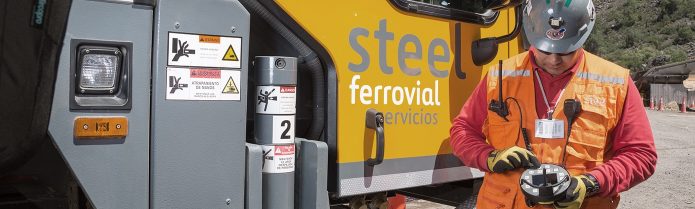
Steel Ingeniería, the mining services company in Chile, has launched the Yo cuido mis manos (I care for my hands) campaign. Within the mining sector a very high percentage of accidents affect the hands. That is why a campaign was launched encouraging the participation of workers, to propose and help implement new ideas for the prevention of accidents to hands.